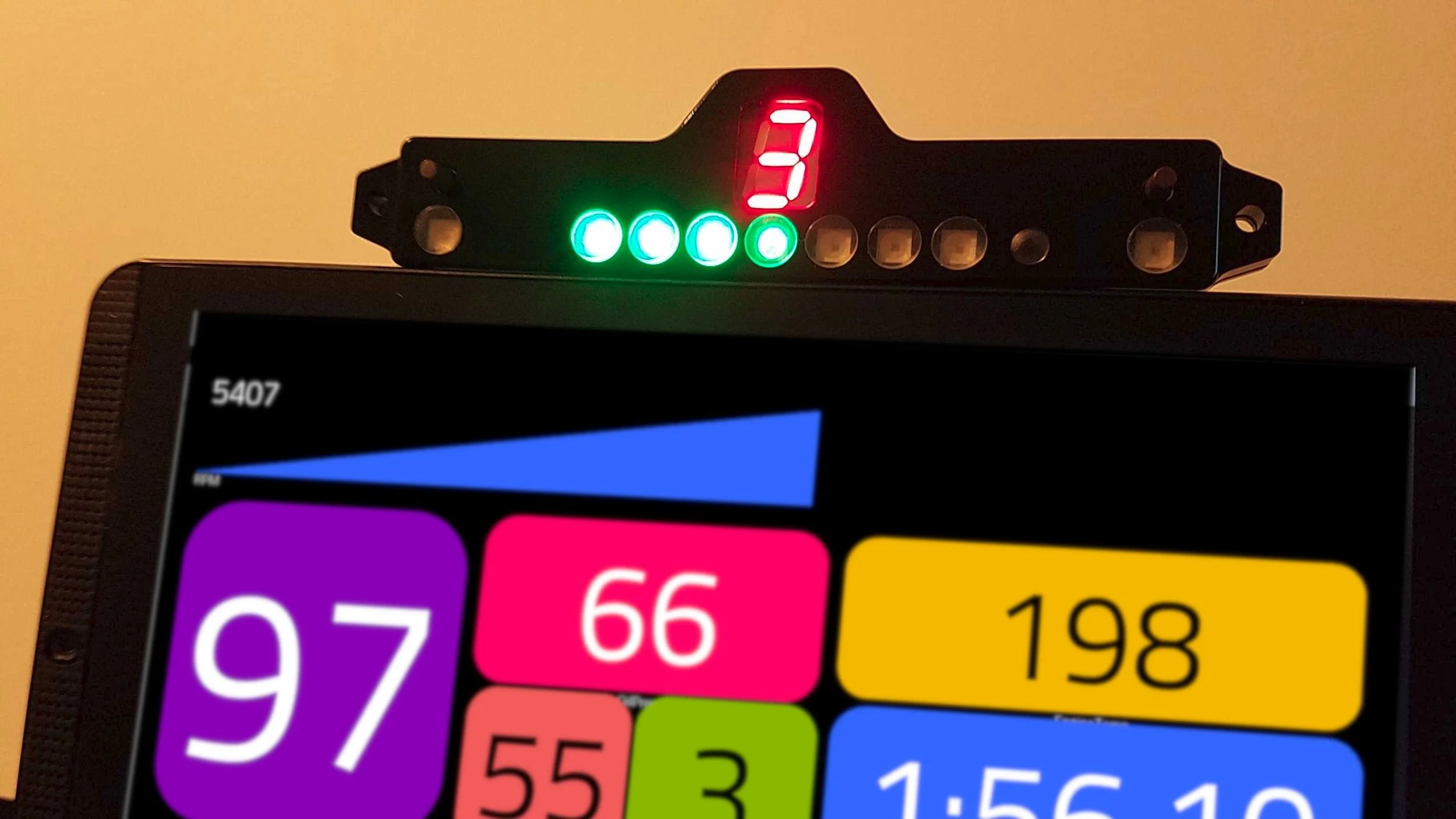
Making the most of your ShiftX3
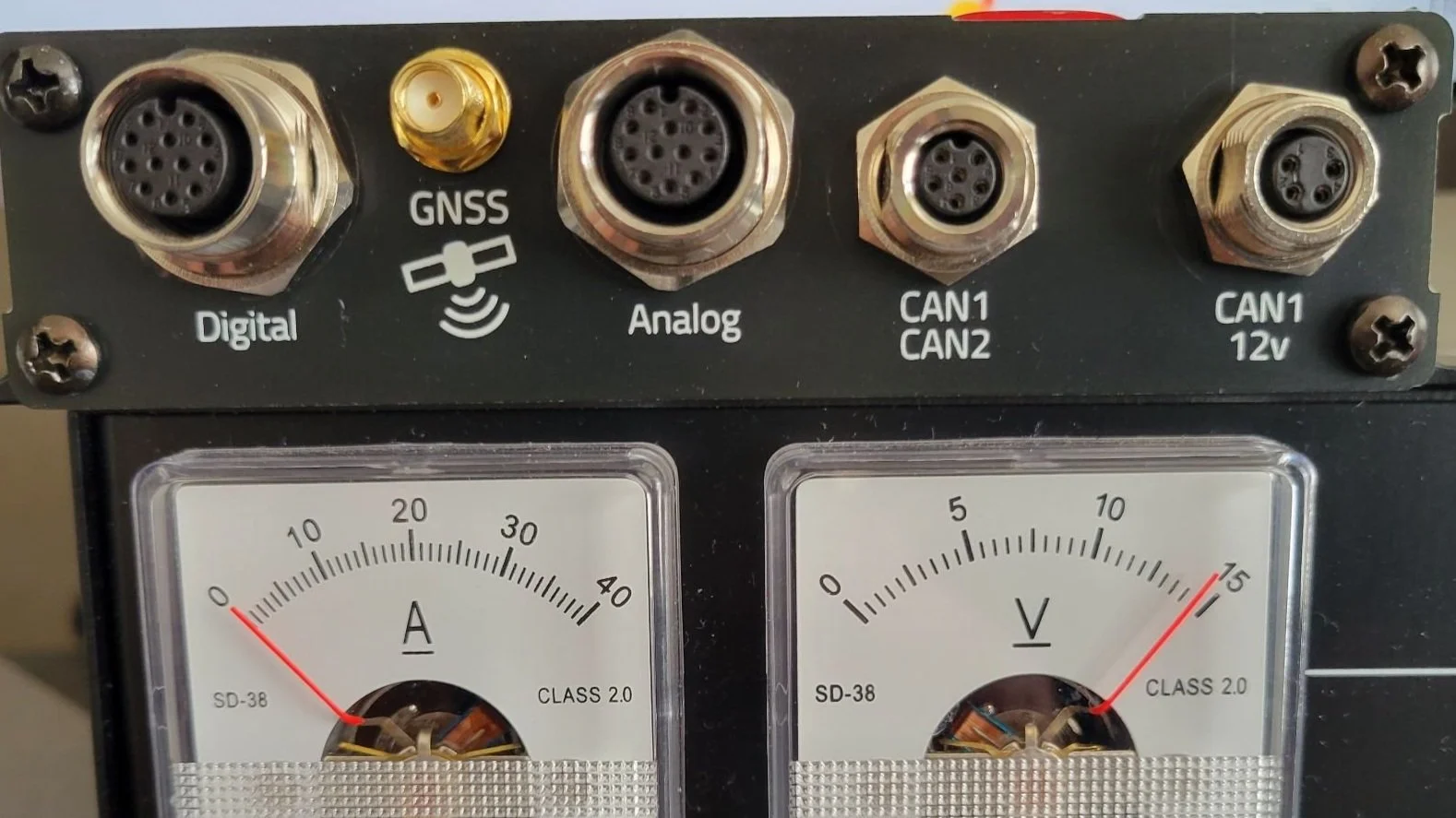
Shopping List
Racing a MK5 Rabbit, AC Compressor
There Are A Few Options For Deleting The AC Compressor, But Are They Worth The Cost?

The Process, Part 3 the Cage
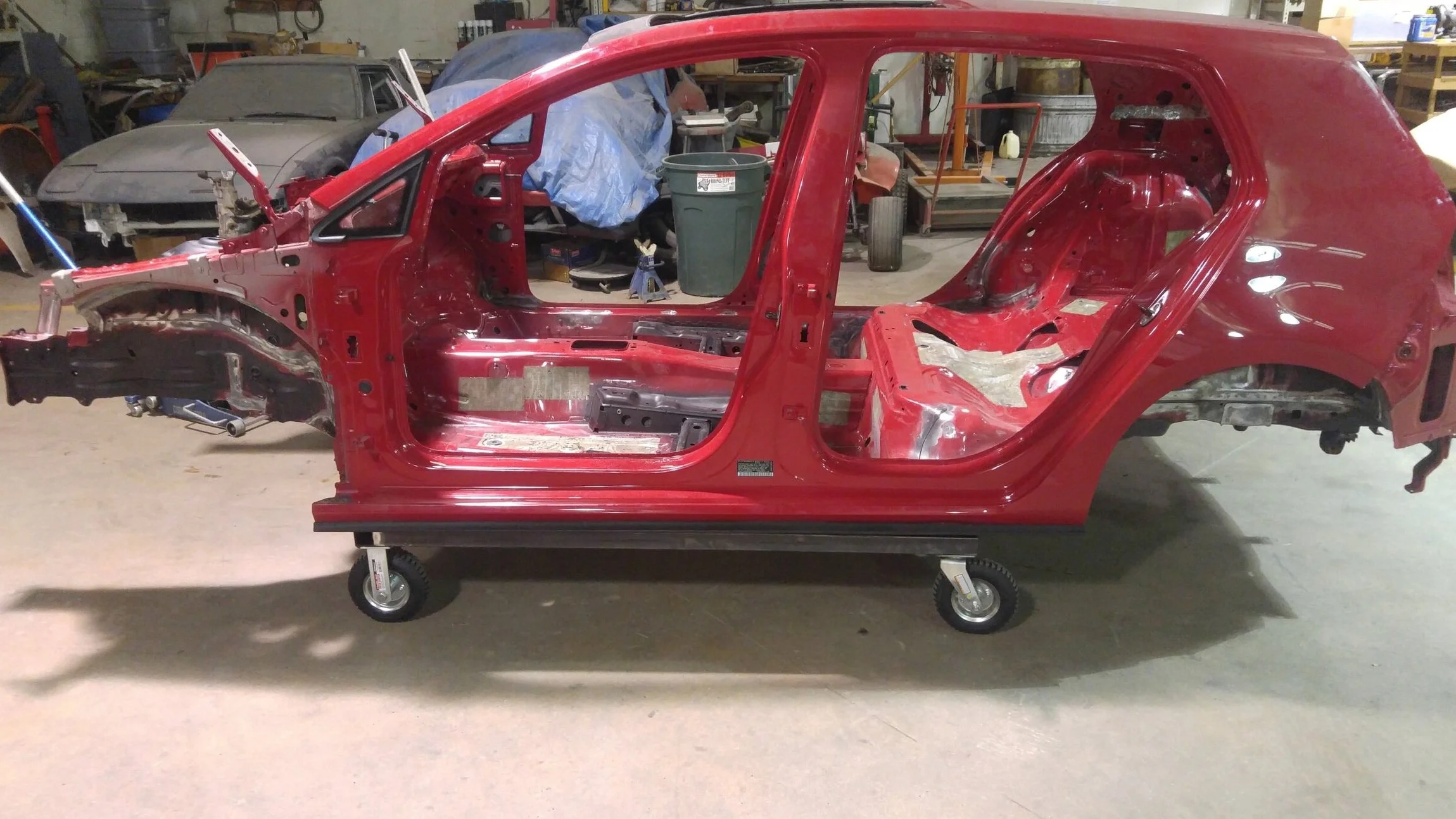
The Process, Part 2

The Process, Production Based Racing Car.

Racing a MK5 Rabbit, Drive Belt issues
Pre-Season Data set-up
When it comes to racing these days, technology comes in the form of data systems, cameras, engine and brake control modules, and even artificial intelligence and machine learning. There is so much to absorb, I love it.
